Podstawy projektowania konstrukcji zoptymalizowanych pod kątem spawania zrobotyzowanego. Przepis na udane spawanie
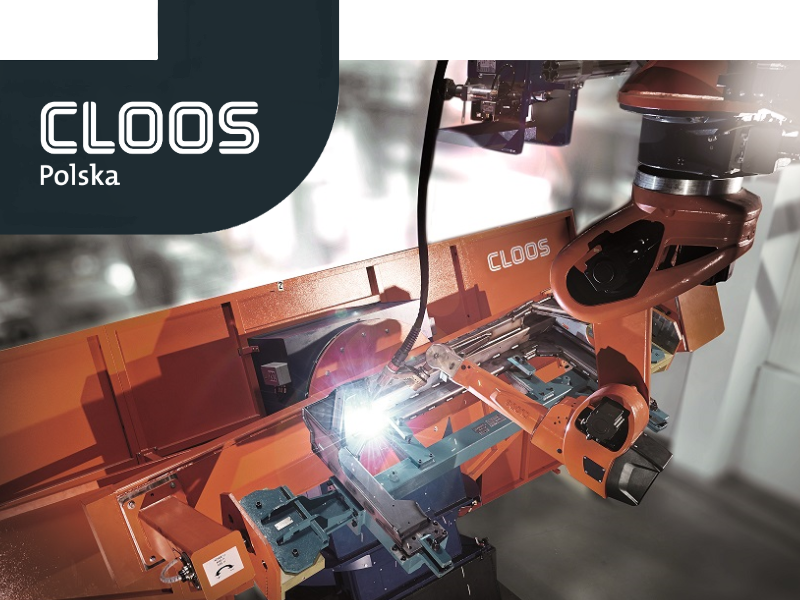
W jaki sposób efektywnie projektować konstrukcje stalowe zoptymalizowane pod kątem spawania zrobotyzowanego? Jakich błędów unikać, a o jakich zasadach pamiętać? W naszym "przepisie" przekrojowo przedstawiamy najważniejsze zasady w omawianym temacie.
1. "Środowisko" czyli interakcja między projektowaniem a produkcją
Projektowanie to opracowanie elementu w taki sposób, aby możliwe było jego wykonanie, w warunkach, w których:- jego funkcjonalność jest gwarantowana,
Konstrukcja z kolei jest łącznikiem pomiędzy ideą dewelopera a możliwościami produkcji.
Odgrywa więc decydującą rolę w powodzeniu rozwoju. Sukces w dużej mierze zależy od komunikacji między zaangażowanymi stronami. Im lepiej projektant jest w stanie pogodzić pomysł dewelopera z możliwościami produkcji, tym mniej wysiłku wymaga wdrożenie.
2. Przygotowanie zrobotyzowanego procesu projektowania konstrukcji stalowych
Dwa najważniejsze stwierdzenia o których trzeba pamiętać na etapie projektowania- ComputerAidedDesign znacznie ułatwia pracę projektanta, ale nie zawsze są brane pod uwagę ważne szczegóły, jak na przykład dane do wykonania spoiny.
- Obecnie wiodącym narzędziem jest rysunek, natomiast dopiero wykonanie modelu sprawi, że możliwości rozwoju w sieci będą nadal wzrastać, a działania przesuną się bardziej w kierunku konstruowania. W praktyce oznacza to, że zwiększy się stopień automatyzacji, a na projektantów zostaną nałożone nowe wymagania. Przy wysokiej komplikacji designu konstrukcji celowym jest symulowanie dostępu palnika spawalniczego na docelowym modelu 3D w celu potwierdzenia dostępności w celu wykonania wszystkich spoin.
Fot. Model spawania konstrukcji
- Wydajność i wytrzymałość funkcjonalna (statyka, dynamika, wymiary komponentów i spoin).
- Wykonalność (dostępność [palnik], osiągalność [spawacz/robot], pozycja palnika, miejsce na spoinę itp.).
- Zasady geometryczne (przepływ siły, brak nacięć, spadki naprężeń, nagromadzenia spoin, przypadki obciążeń).
- Ogólne zasady technologii (odległości od krawędzi, powierzchnie formowane na zimno, przejścia grubości blach itp.).
- Testowalność (oględziny, test PT, test MT, test US, test RT, metody badań niszczących).
- Powtarzalność/ilość rodzajów części.
- Inne (korozja, temperatura przepływu, konstrukcja).
- Rentowność.
Jak ocenić stopień przygotowania do projektowania systemów spawania zrobotyzowanego? Podstawą z pewnością będą twierdzące odpowiedzi na poniższe pytania, które bazują na teorii DFMA. Warto sprawdzić samego siebie i przed przystąpieniem do projektowania wykonać checklistę:
- Jak wyglądają twoje rysunki?
- Czy posługujesz się odniesieniami do aktualnych norm/przepisów?
- Czy wykorzystujesz informacje o projekcie spoiny?
- Czy specyfikacje są jasne?
- Czy specyfikacje są przydatne?
- Czy spawacze rozumieją twoje informacje?
- Czy mówisz tym samym językiem?
- Czy znasz konsekwencje twoich informacji na rysunku?
- Czy tworzysz:
- Instrukcje spawania?
- Plany (sekwencja) spawania?
- Instrukcje testowe?
3. Konstrukcja przyjazna robotyzacji, czyli jaka?
Odpowiedź na powyższe pytanie z pewnością zależy od perspektywy, z której patrzymy w kontekście projektowania.Pamiętajmy, że:
Konstrukcja przyjazna robotom = konstrukcja przystosowana do spawania.
Konstrukcja przystosowana do spawania = spełnione podstawowe zasady spawania.
Dzięki szerokiemu wachlarzowi spawalniczego know-how projektant przyczynia się do optymalizacji produkcji spawalniczej, ale również skupia się na optymalizacji pod kątem obciążeń, optymalizacji pod kątem korozji, optymalizacji pod kątem projektu. Czy są inne obszary, które musi uwzględnić? Odpowiedź brzmi: wszystko zależy od perspektywy. Konstrukcja musi być przede wszystkim poprawna pod względem technologii spawania, zanim będzie można ją zoptymalizować pod kątem robotyki.
Zrozumienie procesu spawania, pozwoli z niego efektywnie korzystać. Projektant musi wiedzieć, jakie procesy spawania są dostępne, znać ich potencjał i dostosować do nich projektowany obiekt. Robot to „tylko” lub aż zmechanizowana wersja ręcznej spawarki, która łączy w sobie różne zalety:
- ciągłość procesu
- większa ładowność
- jakość
- powtarzalność
- odtwarzalność
- brak zmęczenia
4. Specjalne uwagi dotyczące projektu
Przechodząc do praktyki w planowaniu zrobotyzowanego spawania, pamiętaj, że to konstruktor, a nie spawalnik określa położenie spoiny i wymiar spoiny „a”.
Jak zatem obliczyć przekrój czynny spoiny (wymiar a)? Podpowiadamy:
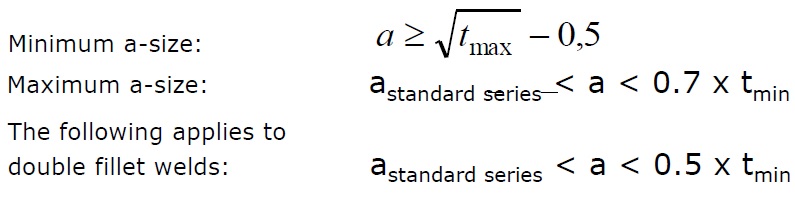
Fot. Wzór na przekrój czynny spoiny
Kolejnym parametrem do ustalenia jest długość spoiny. Spawanie zawsze wprowadza ciepło do elementu, co prowadzi do odkształceń i naprężeń wewnętrznych. Ilość stopiwa jest miarą ilości wprowadzonego ciepła. Dlatego im mniej, tym lepiej!
- Zminimalizuj użycie cienkich i przerywanych spoin tak bardzo, jak to możliwe.
- Unikaj grubych, długich lub ciągłych spoin o dużej ilości wprowadzonego ciepła.
Wartości referencyjne:
Fot. Zalecane z normy wartości długości i przerw spoin pachwinowych
Pamiętaj, że najpierw następuje spawanie kompletnego podzespołu, następnie spawanie całej części.
- najpierw spoiny poprzeczne,
- następnie spoiny wzdłużne.
Unikaj krzyżowania się spoin w celu eliminacji naprężeń spawalniczych (ryzyko pęknięć).
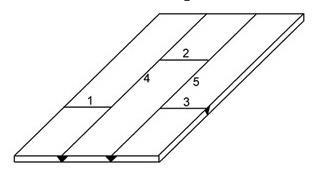
Fot. Jak spawać by unikać odkształceń?
5. Mocowanie i pozycjonowanie detali
Dlaczego sposób mocowanie detalu ma tak ważne znaczenie dla końcowego efektu spawania? Powiązanie to wyjaśnia poniższy rysunek. Widać na nim, że przyrząd mocujący detal do bazy stałej wpływa na pozycję grani spoiny.W korzystnym ustawieniu narzędzia mocującego teoretyczny punkt pozycji grani spoiny pozostaje stały, niezależnie od tolerancji grubości blachy.
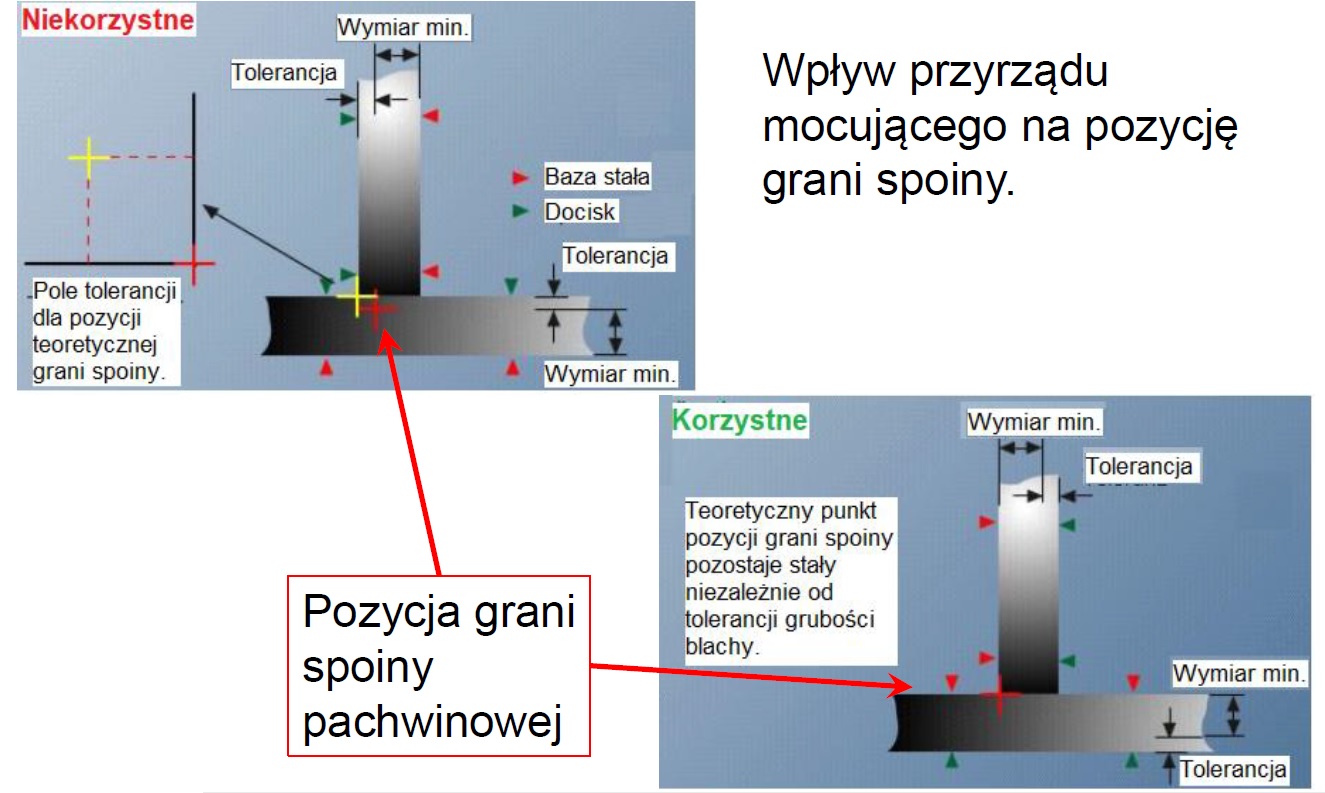
W wytycznych projektanta muszą się znaleźć zalecenia konstrukcyjne dot. dostępu do spawanych elementów i pozycjonowania detali oraz położenia spoiny. Na poniższych rysunkach po raz kolejny przedstawiamy przykłady korzystnych i niekorzystnych rozwiązań.
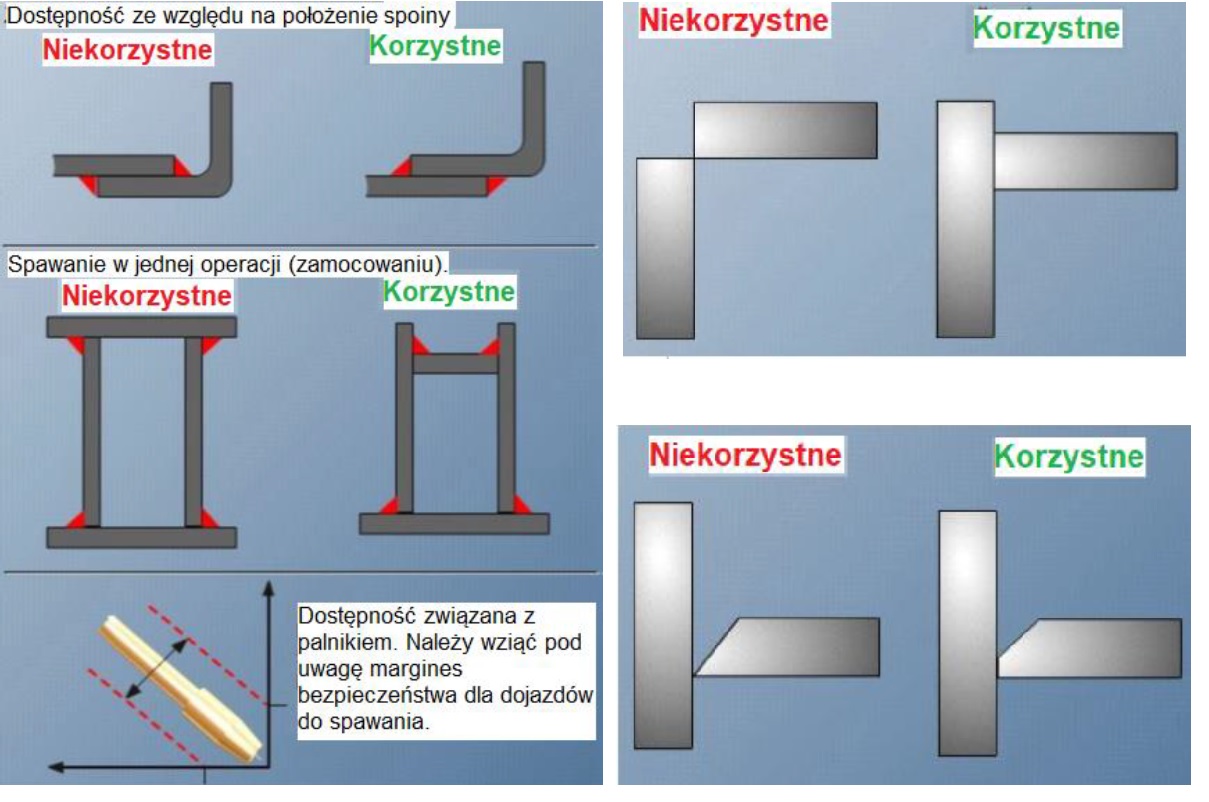
fot. Zalecenia konstrukcyjne dot. położenia spoiny i pozycjonowania detalu
6. Spoiny sczepne – czy warto poświęcać im dużo uwagi?
Bezwzględnie. Spoina sczepna to także spoina, która pełni ważne zadanie w trakcie całego procesu spawania. Jej celem jest utrzymanie poszczególnych elementów spawanych części we właściwej pozycji oraz zminimalizowanie lub zapobieganie zniekształceniom podczas spawania.
Jak prawidłowo wykonać spoiny sczepne?
Spoiny sczepne należy wykonać lub obrobić w takim stopniu, aby podczas spawania uległy całkowitemu stopieniu.
Spoiny sczepne nie mogą być gorszej jakości i muszą być wykonane w takich samych warunkach, jak rzeczywiste spoiny (np. Podgrzewanie wstępne…)
W efekcie końcowym spoina sczepna:
- powinna mieć co najmniej 25 mm długości,
- można ją usunąć przed przegrzaniem,
- może być zawarta w szwie spawalniczym,
- musi być dostosowana do grubości komponentu,
- musi być zeszlifowana i oczyszczona z pęknięć krateru końcowego.
7. Niwelowanie skutków błędów złożenia części, czyli metody kompensacji tolerancji złożenia detali spawanych
W rozwiązaniach CLOOS wyróżniamy dwie główne metody kompensacji tolerancji złożenia detali spawanych: sensory kontaktowe (w spawaniu łukowym są to zazwyczaj czujniki procesu spawania monitorujące prąd i napięcie) oraz optyczne sensory procesu. Umożliwiają one detekcję punktu początku i końca spoiny oraz jej śledzenie przy relatywnie niskich nakładach technicznych.Kontaktowy czujnik elektrodowy
To dzięki niemu w spawaniu łukiem elektrycznym możliwe jest wykrycie odchyłek pomiędzy zapamiętaną ścieżką ruchu, a obecną pozycją uchwytu spawalniczego. Podstawową działania takiego czujnika jest użycie uchwytu jako włącznika w obwodzie elektrycznym, w którym środowisko pracy i elektroda mają przeciwną polaryzację. Kiedy elektroda zbliża się do spawanego elementu, następuje zmiana napięcia w obwodzie elektrycznym, w którym środowisko pracy i elektroda mają przeciwną polaryzację.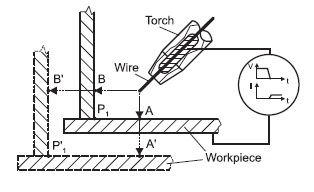
Fot. Sensory kontaktowe
-
Optyczne sensory bezkontaktowe
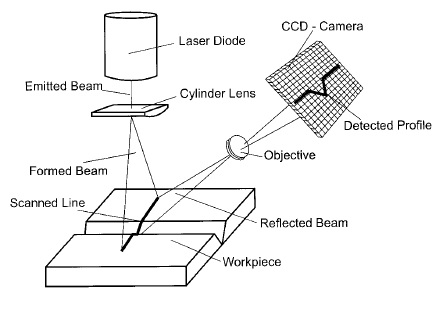
Fot. Optyczne sensory w procesie spawania